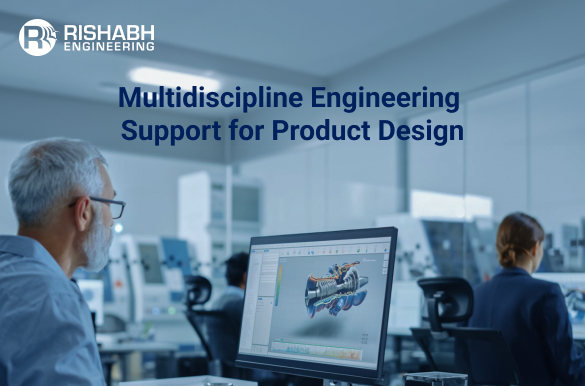
Role of Industrial Product CAD Design in Driving Innovation and Efficiency
|Product design stimulates innovation by influencing sectors’ development of practical, effective, and long-lasting design solutions. Whether it’s an industrial component, a sophisticated consumer device, or a complex plant architecture, a product’s design affects how it looks and how well it works and lasts over time. Businesses must combine cost-effectiveness and competitiveness in a market that moves quickly while meeting strict environmental regulations.
This article emphasizes the value of industrial product design, while providing instances of its effects in the real world and explains how working with multidisciplinary engineering firms like Rishabh Engineering can help streamline the manufacturing processes.
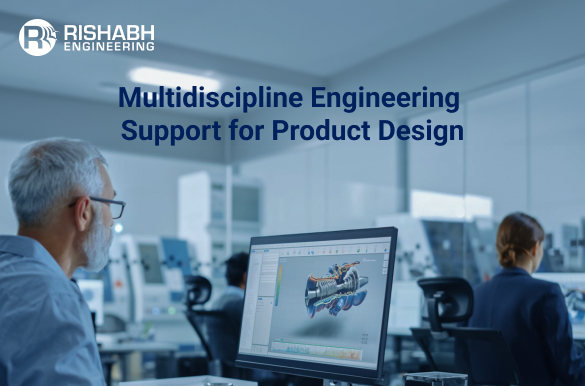
The Essence of Industrial Product Design
Product design is much more than shaping the physical or functional aspects of a product. It is an iterative process where engineering precision meets creativity to solve practical problems. Think about a product as simple as an acoustic enclosure—it’s not just a box to muffle noise; it also ensures safety, durability, and ease of maintenance in a demanding industrial environment.
The role of product design grows when it comes to industrial machinery, modular systems, or expansive plant layouts. It would include designing, developing, and perfecting a product to achieve goals. In sectors such as manufacturing, food processing, oil and gas, and maritime, design links a concept and a dependable, high-performing solution. These designs must also consider industry codes, financial limits, material optimization, and environmental stress.
The goals of product design often revolve around:
- Functionality – Ensuring products meet operational needs and solve challenges effectively.
- Durability – Building components that withstand stress, wear, and environmental conditions.
- Efficiency – Using innovative designs to optimize resource use, energy consumption, and performance.
- Cost-effectiveness – Streamlining production processes to lower manufacturing costs without compromising quality.
Stages Of Industrial Product Design Process
At Rishabh Engineering, we take a structured and comprehensive approach to product design, ensuring every step is optimized for efficiency, durability, and manufacturability.
Here’s a breakdown of the stages we follow:
Ideation Phase
This is where creativity meets strategy. We collaborate with you to generate innovative ideas, exploring possibilities that meet market needs and solve real-world problems.
Key activities during this phase include:
- Brainstorming sessions and idea generation workshops.
- Preliminary sketches and concept exploration.
- Initial stakeholder feedback to refine concepts and identify potential solutions.
Concept Development
In this phase, we refine the ideas into feasible, market-ready concepts. We ensure the designs align with your product vision while considering practicality and functionality.
Key activities during this phase include:
- 3D modeling and detailed sketches of refined concepts.
- Feasibility studies and concept testing to validate ideas.
- Gathering stakeholder feedback to ensure alignment with market demands.
Prototyping and Testing
Turning concepts into physical prototypes is key to validating the design. We build prototypes to test functionality, performance, and usability, ensuring your product is ready for final production.
Key activities during this phase include:
- Building and testing functional prototypes.
- Usability testing with real users for feedback and improvements.
- Iterative testing and design adjustments to meet expectations.
Final Design and Engineering
Here, we finalize the design for manufacturing, focusing on practical production processes and scalability. Our team works with you to ensure the design is optimized for cost-effectiveness and manufacturability.
Key activities during this phase include:
- Developing detailed engineering drawings for production.
- Selecting materials and conducting Design for Manufacturing (DFM) analysis.
- Preparing production-ready documents and collaborating with engineers to optimize the manufacturing process.
Production and Launch
With the design finalized, we will help you transition to production and successfully launch your product. Our team ensures that manufacturing processes run smoothly, quality standards are met, and your product hits the market on time.
Key activities during this phase include:
- Setting up manufacturing processes and quality control measures.
- Planning product launch and marketing strategy.
- Final quality checks and coordination for distribution.
By leveraging our multidisciplinary approach and industry expertise, we help organizations to seamlessly navigate through each phase of product design, turning your vision into a market-ready product that excels in performance, durability, and manufacturability.
How Do Multidisciplinary Engineering Companies Drive Success With Industrial Product CAD Design?
Multidisciplinary engineering companies bring together experts across fields, ensuring that every aspect of product design—mechanical, structural, process, and more—is handled with precision and expertise.
Here’s how this approach can add value:
Specialization with Advanced Software Tools
Modern Industrial Product CAD Design relies on the ability to simulate, visualize, and test ideas before they reach production. Companies like Rishabh Engineering leverage industry-leading tools such as:
- SolidWorks: For high-detail equipment modeling, FEA, and assembly validation.
- Autodesk Inventor: For automated designs with iLogic and plant layout optimization.
- Revit: For 3D visualization and smart family creation in plant layouts.
With these tools, designers can predict performance under real-world conditions, identify design flaws, and refine prototypes—all without wasting physical resources.
Tailored Design Packages to Serve Industry Needs
Every industry has unique requirements. For example:
- Oil & Gas: Equipment like diverter valves or separators must withstand extreme pressure and temperatures.
- Food Processing: Plant layouts must balance hygiene with efficiency.
- Marine Engineering: Hulls and decks require designs that account for seaworthiness and durability.
By understanding these nuances, multidisciplinary engineering companies can customize solutions that align with operational objectives and regulatory standards.
Integration Across Disciplines
Product design doesn’t happen in isolation. Mechanical product design must align with electrical requirements, which in turn must consider structural constraints. A multidisciplinary team ensures that:
- Collaboration between disciplines eliminates silos.
- Designs are optimized for the entire system rather than isolated components.
- Cost overruns due to rework are minimized.
For instance, when designing a modular skid for a process plant, Rishabh’s team ensured that the piping design, structural framework, and electrical routing worked seamlessly, avoiding costly installation delays.
Ensuring Compliance and Safety
Industries subject to stringent safety and compliance regulations (such as ASME and ISO) include oil and gas, maritime, and industrial manufacturing. Designs are guaranteed to be compliant from the start, thanks to the extensive understanding of these standards provided by multidisciplinary firms. This speeds up project completion times and lowers the possibility of regulatory penalties or redesigns.
Efficient Design-to-Production Transition
Bridging the gap between design and manufacturing is crucial for success. Rishabh Engineering supports industrial product CAD design with:
- Designing for Manufacturability (DfM): Creating designs that are practical to produce without compromising quality.
- Providing Detailed Documentation: From exploded views to material specifications, clear instructions reduce errors during assembly.
- Streamlining Communication: Using visualizations and prototypes to keep stakeholders aligned during every phase of production.
Real-World Applications for Industrial Product Design
Multidiscipline engineering companies, like Rishabh Engineering, help tackle diverse product design challenges. Using software tools like SolidWorks, Autodesk Inventor, and Revit, they craft designs that are both precise and practical. Below are some examples that showcase how Rishabh Engineering has delivered exceptional product designs:
Industrial Components Design (Equipment Modeling and Designing)
- Example: Oil coolers, oil separators, and diverter valves.
- Applications: Critical equipment used in the oil & gas industry for fluid and thermal regulation.
- Objective: To deliver reliable and efficient components that ensure minimal downtime and optimized operations.
- Capabilities: SolidWorks for precise 3D modeling, simulation, and performance validation.
- Outcome: High-performing designs tailored to client specifications, ensuring compliance with industry standards.
- Impact: Reduced operational risks, improved energy efficiency, and extended equipment lifespan.
Sheet Metal and Weldment Design
- Example: Acoustic and electrical enclosures.
- Applications: Industrial setups requiring noise mitigation and equipment safety.
- Objective: To provide robust and custom solutions for challenging environments.
- Capabilities: Design expertise in SolidWorks and Autodesk Inventor for sheet metal and weldment layouts.
- Outcome: Durable and efficient enclosures optimized for specific operational needs.
- Impact: Enhanced safety, reduced noise pollution, and improved overall system reliability.
Optimized Structural Support Through FEA
- Example: Piping supports and structural stress analysis.
- Applications: Ensuring mechanical integrity in piping systems across various industries.
- Objective: To identify and mitigate potential failure points through detailed stress simulations.
- Capabilities: Advanced FEA modules in SolidWorks for real-world scenario modeling.
- Outcome: Optimized designs that meet stringent safety standards such as ASME.
- Impact: Increased reliability, prevention of failures, and minimized maintenance costs.
Optimizing Piping and Ducting Systems
- Example: Modular skid systems and plant layouts.
- Applications: Efficient layouts for industrial plants, including food processing and steam exhaust systems.
- Objective: To enhance process flow and reduce material wastage.
- Capabilities: Factory Asset utility in Autodesk Inventor for layout optimization.
- Outcome: Streamlined workflows and layouts that maximize efficiency and minimize operational delays.
- Impact: Improved productivity, cost savings, and better utilization of plant space.
Visualization in Marine Engineering
- Example: 3D modeling for operational and maintenance manuals.
- Applications: Marine components require precise assembly instructions and visual documentation.
- Objective: To provide detailed visualizations for seamless assembly and maintenance.
- Capabilities: Revit and SolidWorks for 3D visualization and exploded views.
- Outcome: Accurate and accessible design documentation adhering to confidentiality requirements.
- Impact: Simplified maintenance reduced operational downtime and improved efficiency.
Real Life Use Cases
Case 1
Case Study: Electrical Box Unit Design for Solar Panel Deployment
Client: A US-based project engineering company
Project Overview:
Rishabh Engineering was tasked with the detailed design and engineering of an electrical box unit for solar panel deployment and machinery integration.
Project Scope:
- Structural Design Report
- 3D Model (internal & external layouts)
- Fabrication Drawings
- Electrical Cable Routing
- Flooring & Ceiling Drawings
- Solar Panel Fixing Mechanism
Project Deliverables:
- Structural Design: Ensured durability using STAAD.Pro.
- 3D Modeling: Optimized layouts with CADWorx & AutoCAD.
- Electrical Integration: Efficient cable routing for compliance and maintenance.
- Fabrication Drawings: Streamlined production with precise documentation.
Outcome:
The project offered delivering a durable, cost-effective, and manufacturable design that met the client’s requirements for seamless solar panel and machinery integration.
Case 2
Case Study: Boosting Cryogenic Plant Efficiency with Optimized Aftercooler Design
Client: A US-based manufacturer of engineered cryogenic gas processing equipment and small-scale process plants for LNG, well services, and industrial gas industries with a strong presence in Southeast Asia.
Project Overview:
The project involved enhancing the thermal efficiency of a cryogenic plant’s cooling system. Rishabh Engineering team helped design the cold turbine aftercooler for the cryogenic plant. The team was tasked with designing and analyzing a Shell and Tube Heat Exchanger for the cold turbine aftercooler, focusing on optimal heat exchange between water and dry air. The client aimed to enhance the cooling efficiency of their plant’s heat exchange system.
Project Scope:
- Thermal Design & Rating: Comprehensive analysis using AspenTech EDR to maximize efficiency.
- TEMA BXM Compliance: Ensured design adhered to international standards.
- Rapid Turnaround: Delivered a detailed thermal design report within two weeks.
Project Deliverables:
- Comprehensive thermal design and rating analysis using AspenTech’s Exchanger Design & Rating (EDR)TM.
- A detailed Thermal Design Report highlighting specifications, simulation results, and performance recommendations.
- Design adherence to BXM TEMA-type standards for industry compliance.
Outcome:
Rishabh Engineering’s tailored design solution improved cooling performance, ensuring durability, compliance, and operational excellence.
Final Words
In a world where modernization propels advancement, industrial product design is essential to the success of all sectors, regardless of size. There are countless opportunities but also myriad difficulties, from building robust industrial machinery to planning effective plant layouts. Rishabh Engineering and other multidisciplinary engineering firms are crucial in this situation. Their focused, detailed engineering services, coupled with varied experience, technological know-how, and dedication to quality, assists the end clients in turning concepts into concrete, marketable goods. You can count on our teams to provide ideas that work, last, and inspire whether you plan a marine component (like marine hull and dec illustration), develop an oil cooler, or optimize a modular skid. Our team is experienced in advancing product design and finding out how you can bring your vision to life.
Looking To Enhance Your Industrial Product Design Process?
Our experts help you create customized design packages using advanced CAD software, ensuring efficiency, durability, and compliance across industries.
Related Blogs
Related Blogs
Detailed Engineering Considerations for Project Success
Engineering projects today require meticulous planning and execution across various…
Navigating the Green Hydrogen Value Chain
Green hydrogen is a powerful contender for a more sustainable…