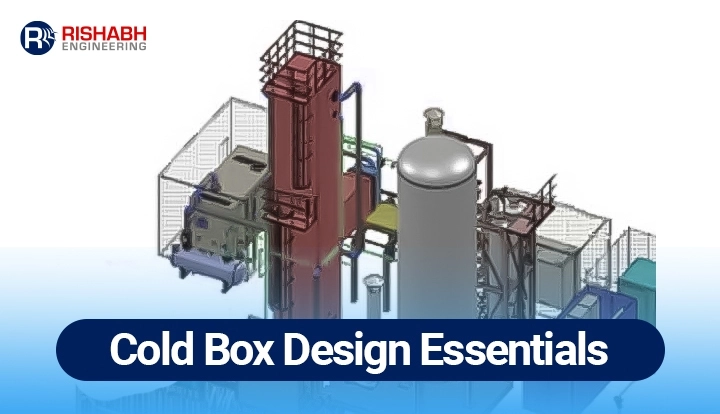
Cryogenic Cold Box Design – Working Principle & Steps
|Within the realm of air separation units, the cold box emerges as a meticulously engineered, large rectangular fortress, supporting the cryogenic process and safeguarding critical cryogenic equipment. Some suppliers prefer a round silo design, where the cold box foundation provides primary support for the enclosed machinery. Welded steel panels compose the cold box wall, establishing a fortified barrier filled with insulating material, ensuring optimal performance of the enclosed equipment.
In this blog, we will discuss the basics of cold box design for cryogenic plants, with its working principle and steps, along with the role of multidisciplinary engineering companies like Rishabh Engineering.
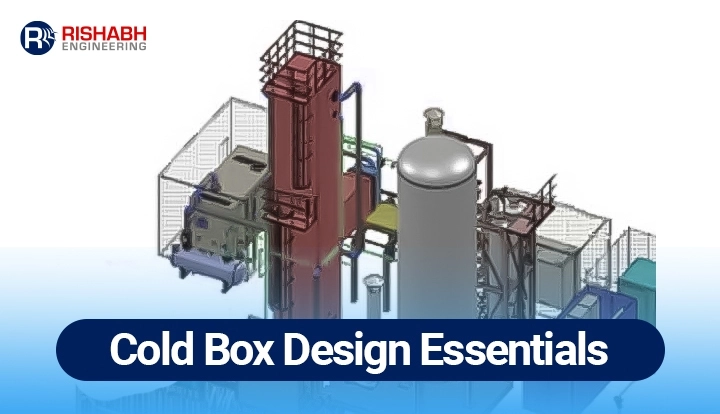
What is a Cold Box?
A cold box is like a ready-to-go unit made of strong carbon steel, kind of like a sturdy outer shell. Inside, it holds special freezing equipment like plate-fin exchangers, core in drums, and all the pipes and instruments that go with it. To keep things cold, they wrap the heat exchanger and pipes with perlite insulation. What’s cold about it is that it’s modular, so it’s easy to set up and won’t take forever. Plus, the company that makes it takes care of all the pipes and instruments, which saves a bunch of time.
Cold Box Design Basics
The cold box frame and foundation undergo meticulous design, tailored to bear the weight of all process equipment, including piping and valves containing the maximum liquid operating level. This design not only adheres to national codes for wind loading but also considers the seismic conditions of its installation location. In air separation plants, the distinctive square columns, strategically placed, are cryogenic cold boxes designed to minimize heat leakage into the environment. The internal temperature of these cold boxes typically hovers around -196°C, with vacuum technology employed to prevent heat transfer.
Other Considerations with Cold Box Design in Cryogenics:
- Insulation in the Cold Box: The insulation material in a cold box can either be perlite, a fine powder, or slag wool, denser than traditional glass wool. Perlite is the choice for insulating most of the cold boxes where access is unlikely. Conversely, slag wool is preferred in areas requiring potential access due to its easier removal. It is commonly used in turbines, pump, and valve boxes.
- Equipment Enclosed in the Cold Box: The cold box serves as a housing for various critical equipment, including distillation columns, heat exchangers, separators, cryogenic adsorbers, piping, valves, and the cold end of the turbine. Associated equipment comprises adsorbers, cryogenic pumps, and expansion turbines. Access to internal equipment during operation is restricted, with functions managed through valves with extended stems, reachable through linked platforms, stairs, or ladders.
- Hazards of Water Entry into the Cold Box: Water entering a cold box presents substantial risks, as it can freeze, impeding piping movement and causing excessive weight loads. Ice formation can significantly prolong the thawing time of a cold box. Thus, maintaining seal integrity at openings, such as valve and piping seal boots and manways, is crucial to prevent water pooling on horizontal surfaces.
- Cold Box Purging: To mitigate hazards like oxygen condensation and ice formation, the space inside the cold box undergoes a nitrogen-filled process known as cold box purge. This is crucial during cryogenic temperatures and is usually maintained during non-operational periods, except during internal work on the cold box equipment.
Types Of Piping In A Cold Box:
Four main types of piping are prevalent in a cryogenic cold box design:
- Process piping: Varying in size, it carries fluids between equipment items.
- Relief valve piping: Connects pressure vessels to external pressure relief valves.
- Purge, vent, and drain piping: Connect process equipment to the outside for services and venting.
- Instrument piping: Connects instruments from outside the cold box to equipment items.
What is the Mechanism to Minimize Leaks & Accommodate Shrinkage Inside the Cold Box?
To minimize leaks, welded joints are utilized in the perlite region, and transition joints between incompatible metals are carefully managed. Shrinkage is accommodated using flexible rubber boots between the cold box surface and valve stems. Warm gas seals are essential for relief valve lines to prevent them from becoming permanently cold. Piping is typically made from aluminum, stainless steel, or copper alloys, ensuring ductility at cryogenic temperatures. Cold box pipes require flexibility to accommodate equipment shrinkage, achieved through a combination of turns and support mechanisms.
What Are The Type Of Valves Used In Cryogenic Systems?
Valves used in cryogenic service have the same functions as in any process but come with additional requirements for low-temperature operation. The valve body is contained within the cold box, with stems extending through the box wall, typically made from stainless steel for strength and low thermal conductivity.
Cold Box Design Working Principle
The design revolves around the principles of thermodynamics and heat transfer. Here’s a simplified explanation of how a cold box typically functions:
- Insulation: The cold box is designed with high-quality insulation materials to minimize heat transfer between the interior and exterior.
- Sealing: The cold box is tightly sealed to prevent the exchange of air between the inside and outside. This helps maintain a consistent temperature inside the box.
- Thermal Mass: Items stored inside the cold box act as thermal mass. When the box is initially cool, these items absorb the cold, helping to maintain a lower temperature over time.
- Refrigeration or Colding Element: Some cold boxes incorporate a cooling element, such as a gel pack or ice pack, to actively lower the temperature inside. This element absorbs heat from the interior, keeping the contents cold.
- Heat Absorption: As the contents of the cold box warm up, heat is absorbed by the cooling element or transferred through the insulation. This process slows down the temperature increase inside the box.
- Ventilation: Proper ventilation may be incorporated to allow excess heat to escape, especially if the cold box is used for transporting items that emit heat.
- External Factors: The external environment also influences the cold box. Exposure to sunlight, ambient temperature, and other external factors can impact the overall efficiency of the cooling process.
- Monitoring and Adjustment: A cold box may include a temperature monitoring system to ensure that the desired temperature is maintained. Users might have to refill the cooling element or tweak settings according to their unique requirements.
- Energy Efficiency: Some advanced cold boxes may use energy-efficient technologies, such as phase change materials or electronic cooling systems, to enhance efficiency and reduce the need for additional elements.
Cryogenic Cold Box Design Steps Followed By Multidisciplinary Engineering Company
Designing a cold box involves a multidisciplinary approach to ensure efficiency and safety. Here are the steps for cold box design followed by a multidisciplinary engineering company:
- Project Definition: Clearly define the objectives, specifications, and requirements of the cold box project, considering temperature ranges, capacity, and intended applications.
- Site Assessment: A thorough site assessment for the cold box installation helps understand a variety of factors including environmental conditions, space constraints, and safety considerations.
- Multidisciplinary Collaboration: Form a collaborative team with a comprehensive approach comprising mechanical, chemical, electrical, and safety engineers to collaborate on the design.
- Process Analysis: Analyze the specific cold storage requirements, considering the type of products to be stored, temperature variations, and potential thermal loads.
- Material Selection: Choose appropriate materials for the cold box construction, considering insulation properties, durability, and compatibility with the stored products.
- Thermal Modeling: Utilize thermal modeling software to simulate temperature distribution within the cold box, optimizing insulation and refrigeration systems for efficiency.
- Mechanical Design: Develop the mechanical design, including structural components, insulation layers, and ventilation systems to maintain the desired temperature levels.
- Refrigeration System Integration: Integrate an efficient refrigeration system into the design, accounting for the specific temperature requirements and energy efficiency goals.
- Electrical and Control Systems: Design electrical systems for lighting, alarms, and control systems to ensure the cold box operates safely and meets regulatory standards.
- Safety Protocols: Introduce safety measures to safeguard both the stored products and personnel. It would include emergency shutdown systems, ventilation controls, and fire suppression.
- Regulatory Compliance: The designed cold box design must comply with relevant industry standards, local building codes, and safety regulations.
- Cost Estimation: The entire project must have a detailed cost estimate. It would include materials, labor, and any additional equipment required.
- Prototype Testing: Creating a cold box prototype requires testing and validation to adjust as required for optimizing performance.
- Documentation: The creation of comprehensive documentation helps for future reference and maintenance. It would include drawings, specifications, and operating manuals.
- Installation and Commissioning: Supervise the cold box installation, making sure all parts are properly connected, and activating the system for smooth operation.
- Training: Train personnel responsible for running and caring for the cold box, with a focus on safety protocols and optimal procedures.
- Monitoring and Maintenance: Set up a monitoring system and routine maintenance plan to guarantee the ongoing efficiency and reliability of the cold box.
Role of Multidiscipline Engineering Companies with Cryogenic Cold Box Design
In the intricate landscape of cryogenic plants and air separation units, the involvement of a multidiscipline engineering company becomes pivotal. Rishabh Engineering, standing out for its proficiency, plays a crucial role in designing and optimizing cold boxes within such facilities. Specifically, Rishabh Engineering’s role includes integrated design solutions, Pipe stress analysis, structural analysis, process optimization, material selection, safety measures, and project management. Their multidisciplinary engineering approach ensures seamless integration, optimal performance, and safety of the cold boxes.
Final Words
The cold box of an air separation unit is the pinnacle of engineering excellence, acting as a fortress safeguarding essential cryogenic equipment. From its painstakingly built frame to the insulating materials used and the incorporation of numerous plumbing systems, every component contributes to the unit’s efficient and safe operation. The engagement of multidisciplinary engineering firms, such as Rishabh Engineering, provides equipment engineering services specialization that comprises a comprehensive approach to optimizing design elements. As technology progresses, the cold box remains a cornerstone in the pursuit of effective air separation operations, with interdisciplinary engineering firms playing an important part in its success.
Looking To Unlock Secrets of Cold Box Design?
We can help you deal with the intricacies of cryogenic design while applying the working principles of cold box and applying multidisciplinary engineering insights.
Related Blogs
Related Blogs
Detailed Engineering Considerations for Project Success
Engineering projects today require meticulous planning and execution across various…
Navigating the Green Hydrogen Value Chain
Green hydrogen is a powerful contender for a more sustainable…