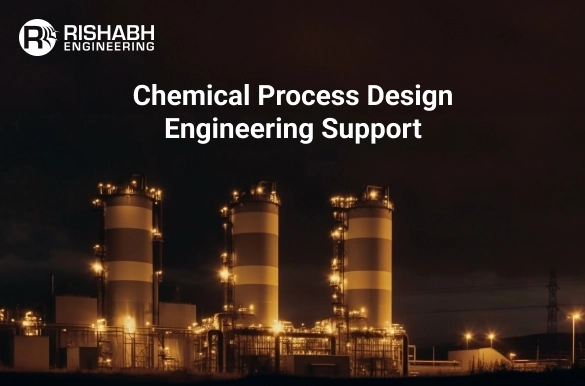
Chemical Process Design: How Multidisciplinary Teams Drive Efficiency
|The foundation of chemical plant operations is process engineering, which guarantees the safe and practical design, implementation, and maintenance of chemical processes. Furthermore, chemical plants nowadays must contend with several difficulties, such as strict regulatory requirements and financial constraints. It takes the process of engineering expertise and fruitful cross-disciplinary collaboration to meet these issues. To maximize design, increase operating efficiency, and guarantee project success, specialists from multidisciplinary teams—such as process, mechanical, electrical, civil, and instrumentation—cooperate.
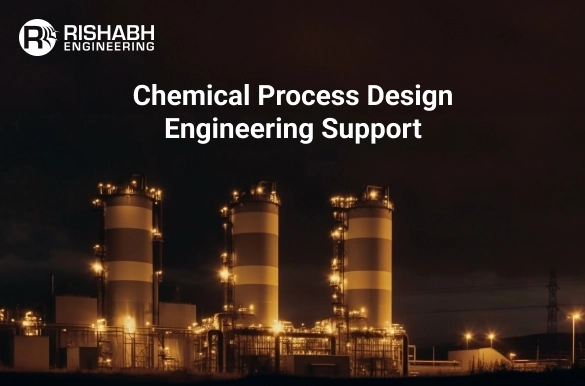
This article covers key objectives, stages, and challenges of chemical process design, emphasizing optimization, multidisciplinary collaboration, tools, and equipment considerations to ensure safe, efficient, and sustainable operations in chemical plants.
What is Process Design in Chemical Engineering?
It involves planning and developing systems that transform raw materials into useful products, such as chemicals, fuels, or medications. To achieve production goals, the emphasis is on creating safe, economical, and efficient processes that minimize risks and expenses while guaranteeing dependable operations.
Key Objectives of Chemical Process Design
Process design plays a key role in ensuring sustainability, safety, and efficiency in chemical plants in the ever-changing field of chemical engineering. A multidisciplinary design engineering firm approaches this holistically, integrating knowledge from other fields to accomplish the following main goals:
Process Optimization for Maximum Output
The primary goal of process design is all about optimizing processes to achieve the highest possible output with minimal input. This involves thorough analysis of chemical reactions, separation processes, and material flow. Using advanced simulation tools like Aspen HYSYS or Pro/II, process engineers model different scenarios to determine the most efficient configurations. A multidisciplinary team modifies variables like temperature, pressure, and flow rates to ensure the chemical plant runs at optimal efficiency, generating consistent product quality.
Ensuring Sustainability and Eco-Friendliness
Sustainability must be a top priority for modern chemical facilities due to mounting pressure to lessen their environmental effects. A diverse team designs procedures that cut emissions, waste, and resource use. This could involve employing green solvents or including energy recovery devices to reduce the environmental impact of the plant. To help the facility maintain compliance with standards like ISO 14001 and lower its overall carbon footprint, environmental engineering experts make sure the design complies with stringent laws while encouraging eco-friendly activities.
Cost Reduction through Energy-Efficient Designs
Reducing operational expenses, especially energy usage, is one of the most important goals in process design. Engineers can pinpoint energy-intensive process phases and recommend improvements by using sophisticated software and modeling tools. For instance, selecting heat exchangers that minimize thermal losses or utilize variable frequency drives (VFDs) for compressors and pumps can significantly lower energy requirements. Engineers from multiple disciplines, such as process, mechanical, and electrical engineers, work together to create industrial packages that support reducing energy consumption and satisfy production goals.
Enhancing Safety in Hazardous Environments
Every element of the plant’s design, from material selection to control system development, adhere to prescribed safety norms by local and global standards. To avoid mishaps, engineers concentrate on creating fail-safe features like air release valves, emergency shutdown systems, and equipment that can withstand explosions. Moreover, automation and electrical engineers collaborate to create reliable control systems that continuously monitor and adjust process parameters, guaranteeing safe operation in real time. By incorporating these safety precautions, the facility reduces the risks of dangerous activities and offers a safe working environment for employees and the community at large.
Stages of Chemical Process Design
Listed below are the stages of chemical process design that help ensure the success of plant’s operation, from concept to full-scale production. An experienced multidisciplinary design engineering company approach each stage with a focus on collaboration, efficiency, and sustainability. Let’s break down these stages:
Conceptual Design:
This is where the initial vision of the project starts to take shape. It involves:
- Preliminary Analysis: The team conducts a thorough assessment of the project’s feasibility, considering factors such as raw material availability, energy sources, environmental impact, and local regulations. Using tools like Aspen HYSYS, we simulate early-stage processes to identify key challenges.
- Feasibility Studies: The input from multidisciplinary teams like process, mechanical, electrical, and civil engineers ensure that evaluation allows achieving project’s technical and financial viability. It involves assessment of project’s long-term sustainability thus focusing on cost projections, timelines, and potential risks.
- Process Selection: It would involve selection of core processes – whether it’s steam methane reforming (SMR), catalytic cracking, or other methods. The engineers collaborate to choose the most effective and cost-efficient process for the plant.
Basic Engineering Design:
Once the project is deemed feasible, here the design engineers define the core structure of the process:
- Process Flow Diagrams (PFDs): It would involve development of detailed PFDs that outline the key stages of the process, including input and output streams, and major equipment like reactors, heat exchangers, and pumps. They serve as the roadmap for the entire system and guide engineers across the next steps.
- Equipment Selection: The mechanical and process engineers work together to select the most suitable equipment based on the process requirements. It would include defining specifications for reactors, heat exchangers, distillation columns, and pumps. Materials, thermal properties, and pressure ratings are chosen based on the requirements of the process and environmental conditions.
- Utility and Energy Balance: In association with electrical and control engineers, our team creates initial energy and utility consumption models to ensure energy efficiency across the plant.
Detailed Engineering Design:
It involves refining every component of the process thus ensuring all aspects are well-defined and ready for implementation:
- Piping and Instrumentation Diagrams (P&IDs): The process and mechanical engineers generate P&IDs that provide detailed schematics of the plant’s piping systems, control loops, instrumentation, and safety devices. Further, they are crucial for visualizing the process flow, potential bottlenecks, and integrating safety measures. P&IDs guide the installation and commissioning phases.
- Equipment Specifications: Detailed specifications for each piece of equipment are created. It would include selection of appropriate materials, sizing, pressure ratings, and identifying critical parts. Mechanical engineers collaborate with process engineers to ensure that the equipment is designed to meet both process and safety standards.
- Operational Guidelines: At this stage, the team prepares operation manuals and guidelines thus ensuring that operators are fully equipped with the necessary knowledge to handle the system safely and efficiently. Electrical and control systems engineers work to integrate real-time monitoring, automation, and safety interlocks for optimal control during operation.
- Safety and Compliance: The safety engineers ensure that the plant design complies with regulatory standards, including OSHA, API, ASME, and local regulations. Further, risk analysis helps identify any potential safety concerns or environmental impact, and corrective measures are incorporated into the design.
- Commissioning Plan: Finally, the experienced engineers create a comprehensive commissioning plan, ensuring that every aspect of the system works as designed before it is handed over for full-scale operation. This includes system testing, fine-tuning of controls, and final safety checks.
Key Aspects of Process Design:
Defining the Steps:
- Outlining each step of the process, from input to output.
- Using visual tools like flowcharts to map out how materials and energy move through the system.
Choosing the Right Equipment:
- Deciding which machines (like reactors, pumps, or heat exchangers) are best for the job.
- Ensuring equipment can handle the required temperatures, pressures, and chemicals.
Balancing Materials and Energy:
- Figuring out how much raw material and energy is needed.
- Making sure there’s no waste or shortage during production.
Safety and Environment:
- Designing processes to handle dangerous chemicals safely.
- Reducing emissions and meeting environmental regulations.
Cost and Efficiency:
- Calculating expenses to keep the project affordable.
- Finding ways to save energy and increase production speed.
Testing and Improving:
- Using software to simulate how the process will work in real life.
- Adjusting avoid problems before building the actual system.
Why Chemical Process Design and Optimization Matter?
A chemical manufacturing company relies on the design and optimization of its chemical processes. They assist businesses in improving the efficiency, safety, and quality of their operations. This explains why they are so crucial:
- Reduced prices: Businesses can lower production costs through process improvement. By identifying and addressing inefficiencies, they can increase production while using less resources. Money is saved when precise energy and materials are used.
- Higher-quality products: Businesses can produce goods that regularly fulfill quality standards by streamlining their operations. As a result, customers are pleased and there are fewer faulty products.
- Increased Security: Early detection of possible risks and mitigation of environmental and worker hazards are two benefits of good process design. Reduced accidents and a safer workplace are the results of safer procedures.
- Environment Protection: Effective processes may reduce waste, save energy, and promote material recycling. This lessens the environmental effect and increases the eco-friendliness of manufacturing.
- Keeping Up Your Competitiveness: Businesses may save costs, create better products, and keep a competitive advantage by using sustainable and effective processes. As a result, they get more customers and make more money.
- Fostering Innovative Thoughts: Designing and optimizing processes also inspires new concepts. To further improve their processes and goods, businesses might experiment with new tools and methods. This encourages creativity and keeps them competitive in the market.
How Do Multidisciplinary Teams Help With Chemical Process Design Engineering?
Engineers from a variety of disciplines, including chemical, mechanical, electrical, and more, frequently make up a process design team. They collaborate to ensure the seamless operation of all plant components, including control systems and pipelines. This teamwork ensures the design meets technical, safety, and business goals. To summarize, process design is all about turning ideas into practical, efficient systems that produce high-quality results in a safe and responsible way.
Challenges in Chemical Process Design and How Multidisciplinary Design Engineering Companies Address Them
Managing complex reactions and guaranteeing the dependability and safety of equipment are only two of the many difficulties that come with designing processes for chemical plants. To tackle these issues, multidisciplinary design engineering firms contribute a range of skills, guaranteeing effective, secure, and economical plant operations.
Managing Complex Chemical Reactions and Separation Processes
Complex reactions and multi-step separations are common in chemical processes, necessitating exact control and optimization to produce the intended results.
Challenges:
- To optimize yields and reduce byproducts, reaction parameters (temperature, pressure, and reactant ratios) must be closely monitored.
- To meet purity requirements, separation procedures such as distillation, crystallization, or extraction require significant energy inputs and exact configuration.
- Variability in raw material properties or process upsets can lead to inefficiencies or compromised product quality.
How Multidiscipline Design Engineering Helps:
- Process Optimization: Aspen HYSYS and Aspen Plus are examples of sophisticated software that process engineers use to model reactions and separations to find the most scalable and effective solutions.
- Custom Equipment Design: To address process requirements, mechanical and chemical engineers work together to design specialized equipment, such as reactors or distillation columns.
- Integrated Control Systems: To ensure stability and optimal performance even under erratic circumstances, electrical and automation experts improve process control with automated systems and real-time monitoring.
Ensuring Reliability and Uptime of Critical Equipment
Unplanned downtime due to equipment failure could impact chemical plant operations – financially & operationally.
Challenges:
- Critical equipment like heat exchangers, pumps, and compressors operate under extreme conditions without frequent maintenance.
- Aging equipment and systems may lead to inefficiencies, breakdowns, or safety risks.
- Balancing maintenance schedules with production demands can be complex.
How Multidiscipline Design Engineering Helps:
- Robust Material Selection: Material specialists ensure equipment could withstand corrosive, high-pressure, or high-temperature environments, extending lifecycle and reliability.
- Enhanced Designs: Structural and mechanical engineers design equipment and layouts to facilitate easy maintenance, minimizing downtime.
Mitigating Risks Related to Hazardous Chemicals and High-Pressure Systems
Safety is a critical concern in chemical plants, particularly when handling hazardous substances or operating at high pressures.
Challenges:
- High-pressure systems are prone to failures like leaks or ruptures, posing significant safety hazards.
- Hazardous chemicals can result in toxic releases, fires, or explosions if not properly managed.
- Compliance with stringent safety regulations (e.g., OSHA, EPA, ISO) is non-negotiable but complex.
How Multidiscipline Design Engineering Helps:
- Safety-First Designs: Engineers incorporate safety features like pressure relief valves, containment systems, and explosion-proof designs into equipment.
- Risk Assessments: Process engineers perform Hazard and Operability (HAZOP) studies and Quantitative Risk Assessments (QRA) to identify and mitigate risks early.
- Regulatory Compliance: Multidisciplinary teams ensure designs meet international codes and standards, such as ASME, API, and NFPA, while aligning with local regulatory requirements.
- Training and Documentation: Engineering companies provide operators with comprehensive training and manuals, improving plant safety awareness and preparedness.
Prominent Software Tools for Chemical Process Engineering Design
Modern chemical plant design relies heavily on advanced software tools that facilitate multidisciplinary collaboration.
Process Simulation:
- Aspen HYSYS: Used for simulating chemical processes and optimizing parameters such as temperature, pressure, and flow rates.
Mechanical Analysis:
- CAESAR II: Conducts pipe stress analysis to ensure mechanical integrity and compliance with ASME B31.3 standards.
- ANSYS and STAAD.Pro: Perform structural analysis to assess equipment and support structures.
Integrated Design Platforms:
- Navisworks: Provides a 3D model review environment, allowing engineers to visualize complex systems and identify potential clashes early in the design process.
Key Equipment Considerations for Multidisciplinary Design Engineering in Chemical Process Optimization
Effective chemical plant operations depend on the thoughtful design and optimization of critical equipment. Multidisciplinary design engineering companies’ approach this with a focus on functionality, safety, and operational efficiency, leveraging expertise across various disciplines.
Heat Exchangers
They play an important role in processes such as heating, cooling, condensation, and evaporation. A design engineering company considers:
- Type Selection: Depending on the process application, efficiency requirements, and operating limits, the right type (such as shell-and-tube, plate, or air-cooled) is chosen.
- Material Selection: To endure elements like corrosion, high pressure, and extreme temperatures, materials such as carbon steel, stainless steel, or specialized alloys are used.
- Thermal Performance: To guarantee energy-efficient operation without sacrificing system performance, thermal efficiency and pressure drop must be balanced.
Reactors
They are central to chemical plants thus driving the transformation of raw materials into finished products. Design priorities would usually include:
- Reaction Kinetics: Designing to maximize yield by understanding chemical reaction mechanisms and rates.
- Heat and Mass Transfer: Ensuring adequate control of thermal and mass flow conditions to maintain optimal reaction environments.
- Safety Features: Incorporating measures to mitigate risks of runaway reactions, overpressure, or operational instability.
Distillation Columns
As a cornerstone of separation processes, distillation columns require precision engineering. Key considerations include:
- Internal Design: Optimizing trays or packing configurations to improve separation efficiency and reduce energy consumption.
- Control Integration: Implementing advanced automation systems to maintain product quality and operational stability.
- Energy Management: Designing for heat integration to improve overall plant energy efficiency.
Storage Tanks
Storage tanks must be designed to handle a variety of chemical substances safely and efficiently. Key factors are:
- Material Compatibility: Ensuring the tank material resists chemical reactions with stored substances.
- Safety Systems: Including features like pressure relief valves and secondary containment to prevent accidents.
- Structural Integrity: Accounting for environmental conditions, such as seismic activity or extreme temperatures, during the design phase.
Additionally, by integrating the knowledge of structural, mechanical, electrical, and process engineers, multidisciplinary design engineering firms guarantee that every piece of machinery is optimized for sustainability, efficiency, and safety. Additionally, this integrated strategy reduces risks and promotes long-term cost savings for chemical facilities in addition to improving operational efficiency.
Final Words
To sum it up, maximizing operations, guaranteeing safety, and encouraging innovation in chemical plant functionality all depend on a chemical process design approach. Process engineering services facilitate resource usage, maintain industry compliance, and provide sustainable solutions that are customized to meet specific operational demands by utilizing a multidisciplinary approach and integrating cutting-edge technologies. The emphasis on chemical process design is crucial as industries change since it offers dependable, economical, and progressive solutions that enable companies to attain both strategic expansion and operational excellence.
Looking To Optimize Your Chemical Plant Operations?
Our team supports you with designing specialized engineering packages that enhance efficiency and sustainability.
Related Blogs
Related Blogs
Process Modeling & Simulation Using AspenTech Software in Multidisciplinary Engineering
For the ever-evolving world of industrial processes and engineering, the…
Navigating the World of Process Engineering with Rishabh Engineering
Process engineering can be considered the foundation for modern manufacturing,…