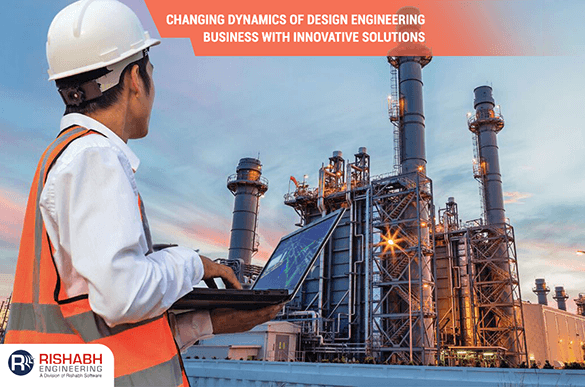
Changing Dynamics of Design Engineering Business With Innovative Solutions
|The oil & gas industry has always been the center of the global economy. Its demand and supply matrix always impacts the prices of the commodity across the globe. Adding to already complex trade is the geographical location of reserves, as approximately 60-70% of it is located in the Middle East and African countries. And the geopolitical situation in these countries has always created a challenging situation for the market. It has also been observed lately that the cost of production per barrel is decreasing. But this is not an easy lesson learned considering the great depression in the industry that has made all the major producers cautious of the production cost.
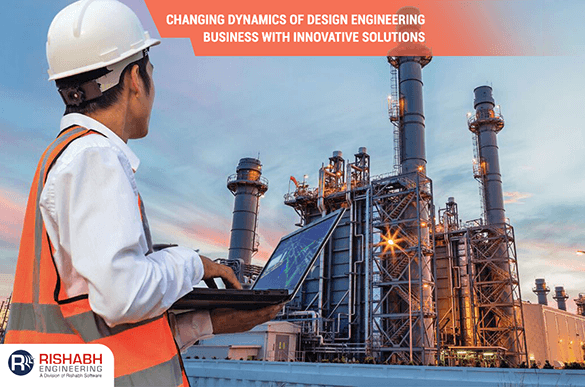
Here are some of the changes witnessed;
Technological Advancement and Reduction In Production Cost
Over the decade we have seen a huge change in the brent prices. From as high as approx. USD 120 / barrel to as low as USD 26.81/ barrel. And it is in the timeframe of a decade (from 2011 to 2021). This suggests that the industry is highly volatile and multiple factors are affecting the cost of the crude. Now, considering the past historical data all the major producers have become cautious with capital spending. There have been numerous attempts with huge investments to develop technologies that could help reduce the overall production cost per barrel. This has however impacted the entire value chain.
Oil & Gas Value Chain
There is also a significant change in project planning and investment strategy. It is pushing for the need to get stringent cost control and effective delivery in place to meet the demand and maintain the project viability.
Here’s how the ecosystem is changing:
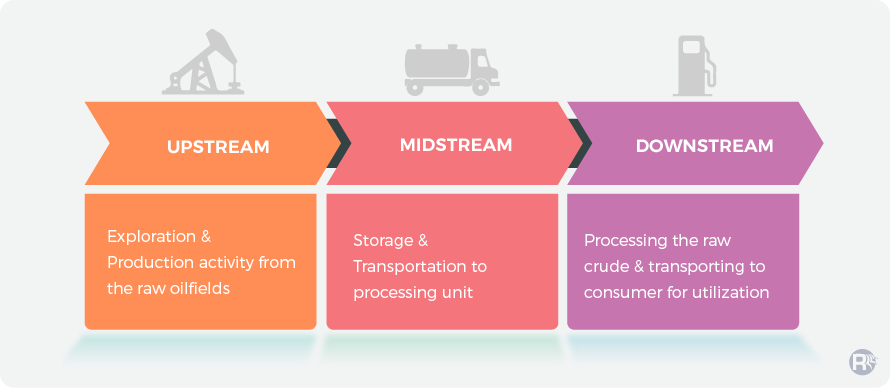
While we see the cost of overall brent changing drastically, the complete value chain must be cost-effective to offer sustainability in the market. And, the failure of any of the assembly from the above three phases would result in a direct impact on the creation of a dynamic organization and become vulnerable to industry changes that impact the global economy. For example, considering the recent event with the start of the global pandemic there was a sudden decrease in the demand for the Brent as the consumption decreased drastically. It resulted in a massive wait for on-shelf products to be delivered. To add to this mix, the storage available across the globe had reached its maximum capacity while the production output from the well was still being pumped out. The outcome with a steep decline in the Brent prices resulted in huge losses to the company.
Way Forward
Based on many such events, it is evident that companies need to devise new strategies to address this scenario. For instance, a major oil producers in the USA and Europe region have come up with the option of developing “global engineering offices”. To control the overall cost across projects during the FEED and Detail Engineering Phase, it has been made mandatory by some of the major operators to use Offshore development partners from the Asia pacific or the African region.
The benefits which can be foreseen for using these offices are as follows.
- 20-35% reduction in overall engineering cost
- Quick TAT in the project execution
- High-quality deliverable at reasonable prices
- Availability of high skill resource pool
The four points mentioned above are driving the requirement for the utilization of the Engineering center based out of Asia Pacific. Rishabh Engineering is one such organization well-positioned to help OEM, Fabricators, Engineering consultants and EPC & EPCM for Plant detail design and engineering services across the various discipline. We’ve been working for the last 14 years with ARAMCO, BASF, SABIC, IOCL, SHELL, DOW, BP & many other oil producers as our clients, providing strategic benefits, quality deliverable & new business opportunities.
For instance, we were recently approached by one of the engineering consultants based out of Baton Rouge for one of their Retrofit projects. It was in a critical stage for modification of the Acetylene complex. They wanted to replace the heat exchanger with jet injectors using point cloud data. Our team swiftly completed the overall project activity. It helped reduce the engineering cycle by 3 weeks. And, by developing a time-frame overlap with the US offices, we helped the customer with seamless management of engineering production for approx. 18-19 hours/day without any variance.
With this deep technical understanding and prowess of managing varied projects, our team got the opportunity to work on future assignments. As part of this, we continue to enable organizations meet the strategic benefits in terms of overall quality, timeline, and cost.
If you wish to learn more about our capability and how do we deliver please drop us a line to discuss in more detail.
Related Blogs
Related Blogs
Meet Rishabh Engineering at ADIPEC 2012 for Potential Partnerships in Engineering Support Solutions
Rishabh Engineering, a multi-disciplinary engineering support division of Rishabh Software,…
Norway Opens New Arctic Area to Oil Drilling While U.S. Drilling Drops & Canadian Drilling Increases
Recently, the Parliament of Norway voted to open up a…