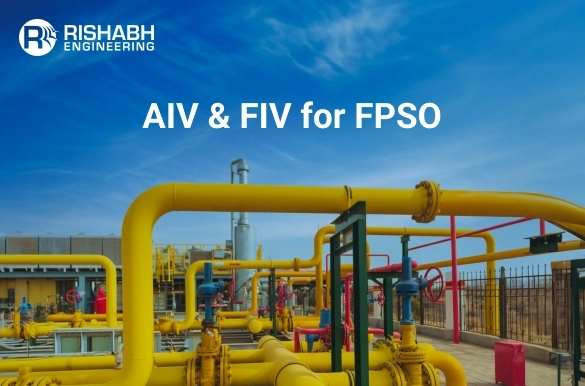
Acoustic & Flow Induced Vibration Analysis for FPSO
|FPSO (Floating Production Storage and Offloading) units are crucial for offshore oil and gas production. These ships encounter numerous challenges when operating in harsh maritime conditions, including managing vibrations in their piping systems. Engineers must deal with two basic vibration types: acoustic-induced (AIV) and flow-induced (FIV) vibrations. Insufficient control of these vibrations may lead to fatigue issues in pipelines, supports, and other equipment. Severe system failures, unplanned outages, and expensive repairs could result from this. Finding and reducing these hazards is essential to the dependability and security of FPSO operations.
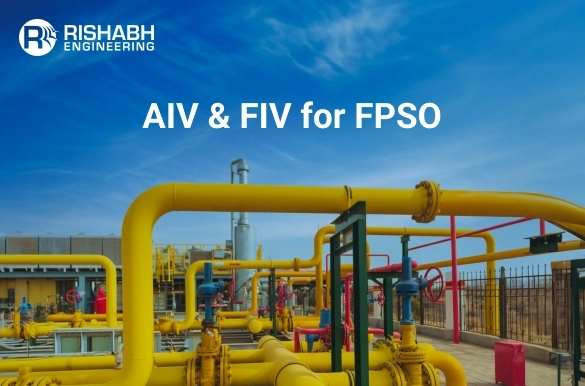
We’ll go over what is flow induced and acoustic induced vibration analysis, how it impacts FPSO projects, and how a multidisciplinary design engineering firm like Rishabh Engineering can assist lower these risks.
What is Acoustic Induced Vibration (AIV)?
AIV describes vibrations caused by high-frequency acoustic energy generated by pressure fluctuations in fluid systems. It is a result of sudden changes in flow caused by parts like flow regulators, control valves, or pressure relief valves. When high-energy sound waves strike pipe walls, especially those with thin walls, they can produce powerful vibrations. Inadequate control of these vibrations can lead to leaks, fatigue failures, or even catastrophic damage to FPSO units.
The Challenge of Acoustic Induced Vibration in FPSO Operations
FPSOs, due to their compact and integrated design, house extensive piping networks that operate under high pressure. The risk of AIV is heightened in these environments due to the presence of various flow-modulating devices. The potential consequences include:
- Fatigue Damage: Prolonged exposure to high-frequency vibrations can create structural fatigue by weakening flanges, welded sections, and pipe joints.
- Operational Downtime: Unplanned maintenance brought on by AIV-induced malfunctions may cause production to stop, resulting in expensive delays.
- Safety Hazards: Employees aboard the FPSO may be at risk if the systems’ integrity is jeopardized.
AIV Analysis Techniques
To identify and mitigate AIV risks, engineers employ advanced simulation tools and methodologies:
- Acoustic Simulation: To forecast possible vibration hotspots, the propagation of acoustic waves within piping systems is modeled using Computational Fluid Dynamics (CFD).
- Finite Element Analysis (FEA): This method determines areas that are prone to fatigue by evaluating the structural response of pipes to high-frequency acoustic sound.
- Modal Analysis: It is used to identify the inherent frequencies of piping systems and make sure they do not overlap with the frequencies produced by acoustic waves.
Mitigating Acoustic Induced Vibration In FPSO Projects
- Design Optimization: Using thicker-walled pipes and reducing flow turbulence through straightening vans or diffusers can significantly reduce AIV risks.
- Enhanced Supports: Installing additional bracing and supports in vulnerable areas helps absorb and dissipate acoustic energy.
- Advanced Flow Control: Implementing silencers or noise-dampening devices on high-pressure valves can mitigate the generation of acoustic waves.
What is Flow Induced Vibration (FIV)?
Flow Induced Vibration (FIV) arises when fluids in pipelines flow turbulently, particularly around curves, elbows, or constraints, flow-induced vibration, or FIV, results. These regions create vortices as fluids flow through them, creating alternate forces that press against the pipe walls. If the flow velocity reaches certain critical thresholds, these forces can generate vibrations that can damage piping systems and equipment.
The Impact of FIV on FPSOs
FPSOs are particularly vulnerable to FIV due to their confined space, extensive piping systems, and high flow rates. FIV can manifest in several detrimental ways:
- Piping Fatigue: Continuous exposure to flow-induced vibrations can lead to fatigue cracks, which may cause leaks or ruptures.
- Equipment Damage: Excessive vibrations can shorten the lifespan of critical components like compressors, heat exchangers, and pumps.
- Production Interruptions: Damage caused by FIV may require unscheduled maintenance, leading to costly downtime.
FIV Analysis Techniques
Addressing FIV involves a combination of predictive analysis and real-time monitoring:
- CFD Analysis: Used to model fluid flow behavior, helping engineers understand where turbulence and vortex shedding are likely to occur.
- Piping Stress Analysis: Tools like CAESAR II are used to evaluate the stress distribution within piping networks, identifying sections prone to FIV.
- Dynamic Vibration Testing: Conducting tests on actual systems to validate simulation results and identify unanticipated FIV sources.
Mitigating Flow Induced Vibration in FPSO Projects
- Streamlined Piping Layout: Reducing the number of elbows, tees, and fittings helps decrease flow disturbances, thus lowering FIV risk.
- Flow Conditioning Devices: Installing diffusers, flow straighteners, and control valves designed to minimize turbulence can reduce vibration.
- Structural Reinforcement: Adding vibration dampers and supports can help manage the energy transferred from turbulent flows, protecting sensitive equipment.
Role of Multidisciplinary Design Engineering in Managing AIV and FIV for FPSO
A holistic, multidisciplinary approach is essential to address FPSO vibrations effectively. Multidisciplinary design engineering firms, such as Rishabh Engineering, provide FPSO operators with dependable solutions to improve operational safety and efficiency by offering a full range of services, from simulation and analysis to design optimization and execution.
Key Contributions of Multidisciplinary Engineering
- Integrated Vibration Analysis: Multidisciplinary engineering teams leverage advanced simulation tools (e.g., CAESAR II for piping stress, ANSYS for dynamic analysis) to model and predict vibrational behaviors in FPSO systems. By identifying the root causes of AIV and FIV, these simulations enable engineers to devise precise mitigation measures.
- Collaborative Design Optimization: By combining expertise across piping, structural, and mechanical disciplines, multidisciplinary teams can develop optimized designs that reduce AIV and FIV risks. Because of Rishabh Engineering’s experience with FPSO projects, for instance, its teams can assess pipe supports, implement dampening devices, and suggest layout modifications that reduce vibrational impact while respecting FPSO space limitations.
- Material and Structural Recommendations: The materials used largely determine how vibrations are transferred and attenuated. Multidisciplinary engineers can suggest materials with improved damping qualities or modified geometries to lower vibrational energy. Structural experts work alongside material scientists to determine the best combination of pipe wall thickness, material properties, and layout configurations to mitigate vibrations.
- Field Verification and Troubleshooting: Addressing AIV and FIV effectively require field verification to confirm simulation results and troubleshoot unanticipated issues. Rishabh Engineering’s multidisciplinary teams are equipped to provide on-site inspections, assess vibration symptoms, and implement corrective measures that align with real-world conditions, which are particularly valuable in FPSO environments where unforeseen issues often arise.
- Guidance on Industry Standards and Compliance: Strict industry standards, including ISO, API, and DNV-GL, which deal with fatigue limits and vibration, must be followed by FPSO projects. In-depth knowledge of these standards is provided by multidisciplinary design firms, which help operators guarantee compliance and lower the possibility of expensive non-conformances.
How Can Rishabh Engineering Help Mitigate AIV & FIV Risks?
Rishabh Engineering, with its expertise in multidisciplinary design engineering, is well-positioned to assist clients in addressing AIV and FIV challenges for FPSO projects.
Here’s how our team can help add value:
- Comprehensive Piping Stress Analysis: Rishabh utilizes advanced software tools like CAESAR II and ANSYS to perform in-depth piping stress analysis. This helps identify areas at risk of AIV and FIV and optimize designs to mitigate these risks.
- Flow Dynamics & Acoustic Analysis: With experience in CFD simulations, Rishabh can assess flow conditions and predict vibration behavior. This enables early detection of potential AIV and FIV issues, allowing for design adjustments before fabrication.
- Structural Reinforcement Design: Rishabh can provide vibration-damping solutions and structural reinforcements using programs like STAAD.Pro to shield vital components from harm caused by vibration.
- Integrated Multidisciplinary Approach: FPSO projects necessitate knowledge of various engineering specialties, including mechanical, structural, and piping. To ensure that all facets of AIV and FIV are considered, Rishabh’s team offers a comprehensive approach to design and analysis.
- Offshore Environment Design Optimization: Rishabh guarantees that its clients’ FPSO systems are optimal for safety, dependability, and longevity by utilizing industry standards, expertise, and best practices in offshore engineering.
Case Study: Rishabh Engineering’s Success in Addressing AIV & FIV
For one of its clients, a leading EPC company operating an FPSO off the coast of West Africa, Rishabh Engineering, was tasked with detail engineering & procurement support for Gas Pipeline Project. As part of the process, a comprehensive vibration analysis was conducted on critical pipelines. The project involved:
- Assessing High-Risk Areas: Using CAESAR II to identify sections of the pipeline prone to AIV and FIV.
- Simulating Flow Behavior: Applying CFD tools to analyze flow profiles and acoustic resonance risks.
- Implementing Mitigation Measures: Designing additional supports and implementing flow straighteners to reduce turbulence-induced vibrations.
- Continuous Monitoring Plan: Establishing a monitoring system to ensure real-time detection of potential vibration issues.
The results included a significant reduction in maintenance costs and downtime, along with enhanced safety for the FPSO operations.
Final Words
As offshore projects get more complicated and run under more pressure, AIV and FIV become crucial considerations in the design and operation of FPSO units. Deep knowledge of fluid dynamics, structural analysis, and acoustic behavior are necessary to meet these issues.
A multidisciplinary design engineering firm, like Rishabh Engineering offers combines the knowledge and resources required to assess, forecast, and reduce the risks associated with AIV and FIV. Our piping stress analysis services team ensures the safety, dependability, and performance optimization of its clients’ FPSO projects by fusing sophisticated technical analysis by utilizing leading software tools to design industrial packages.
Seek Help With Piping Engineering?
Our team offers expert design, analysis, and consulting services for developing efficient, safe, and compliant industrial packages.
Related Blogs
Related Blogs
Piping Support Design and Engineering
Pipe support design is an important component of piping engineering…
Detailed Engineering of Piping Systems
Detailed engineering involves design, detail, engineering and layout of piping…